Sklejka (Plywood) i płyta OSB (Oriented Strand Board) to dwa najpopularniejsze drewnopochodne płyty konstrukcyjne stosowane w budownictwie i wykończeniach. Oba materiały są cenione za wysoką wytrzymałość, sztywność i wszechstronność zastosowań – od poszyć ścian i dachów w systemach szkieletowych, przez podłogi i stropy. Mimo wielu cech wspólnych, sklejka i OSB (szczególnie OSB/3) różnią się budową oraz właściwościami, co sprawia, że każdy z nich lepiej sprawdza się w nieco innych warunkach. W poniższym poradniku porównujemy OSB/3 vs sklejka w kontekście prefabrykacji budowlanej i tradycyjnych konstrukcji – omawiamy różnice w wytrzymałości, obróbce (także na liniach CNC), odporności na wilgoć, paroprzepuszczalności, emisji formaldehydu, reakcji na ogień, aspekty ekologiczne (ślady węglowe), zalecenia montażowe, dostępne formaty i ceny. Dzięki temu dowiesz się, który materiał wybrać do konstrukcji i wykończenia – czy lepsza będzie sklejka, czy płyta OSB – w zależności od potrzeb Twojego projektu, skali produkcji (prefabrykacja maszynowa) oraz oczekiwanego standardu (ekonomiczny vs premium).
Sklejka a płyta OSB – podstawowe różnice i zastosowania
Sklejka to warstwowa płyta z fornirów (cienkich arkuszy drewna) klejonych naprzemiennie pod kątem 90°. Taka krzyżowa struktura nadaje sklejce wysoką stabilność wymiarową i wytrzymałość w obu kierunkach. Sklejki mogą być wykonywane z różnych gatunków drewna (liściaste – np. brzoza, buk, olcha; iglaste – np. sosna, świerk), a także z wykorzystaniem różnych spoiw klejowych w zależności od przeznaczenia (np. kleje suchotrwałe do wnętrz, wodoodporne typu WBP do zastosowań zewnętrznych). Sklejka od lat jest materiałem uniwersalnym – używana zarówno w budownictwie (np. poszycia ścian działowych, poszycia dachów, podłogi, elementy konstrukcji szkieletowych), jak i w przemyśle meblowym, transportowym, szkutnictwie czy do celów dekoracyjnych. Dzięki naturalnemu rysunkowi drewna i gładkiej powierzchni, sklejka bywa też wybierana, gdy ważna jest estetyka wykończenia.
Płyta OSB to kompozytowa płyta drewnopochodna wytwarzana z długich wiórów drzewnych (zwykle świerkowych lub sosnowych) ułożonych warstwowo: w zewnętrznych warstwach wióry są zorientowane wzdłuż dłuższego wymiaru płyty, a w wewnętrznej – w poprzek. Najczęściej spotykane OSB to trójwarstwowe płyty o dość jednorodnej strukturze i kierunkowej wytrzymałości. OSB zostały zaprojektowane jako tani, lecz mocny zamiennik litych desek – są pozbawione wad naturalnego drewna (sęków, pęknięć) i cechują się równomierną gęstością oraz odpornością na paczenie. W budownictwie najpopularniejsza jest OSB3 – płyta nośna przeznaczona do zastosowań w warunkach wilgotnych (klasa użytkowania 2 wg EN 300). Standardowe zastosowania płyt OSB3 to poszycia ścian, dachów i podłóg w domach szkieletowych, poszycia szalunkowe, podkłady podłogowe itp. Ze względu na przystępną cenę i łatwą obróbkę, OSB często wykorzystuje się przy realizacji ekonomicznych, masowych projektów budowlanych lub jako zamiennik sklejki w mniej eksponowanych elementach.
Kluczowe różnice: Sklejka ma zazwyczaj wyższą wytrzymałość ogólną (w zależności od gatunku sklejki nawet 150% wyższą np. na zginanie statyczne) dzięki wielowarstwowej konstrukcji i lepiej znosi obciążenia dynamiczne (udarowe). Płyta OSB jest nieco bardziej kierunkowa – bardzo sztywna i wytrzymała wzdłuż głównej osi (wióry zewnętrzne), choć słabiej niż sklejka przenosi siły w poprzek. OSB jest też z reguły cięższa na m² dla tej samej grubości (większa gęstość w porównaniu do sklejki sosnowej grubowarstwowej, choć sklejka brzozowa może być gęstsza od OSB). Sklejka wyróżnia się również lepszą odpornością na wilgoć (szczególnie jeśli użyto klejów wodoodpornych) oraz atrakcyjniejszym wyglądem powierzchni. Z kolei OSB ma przewagę w cenie i dostępności – jest znacząco tańsza i produkowana w większych formatach płyt. Poniżej przedstawiamy szczegółowe porównanie obu materiałów pod kątem najważniejszych parametrów istotnych w prefabrykacji budowlanej i pracach konstrukcyjno-wykończeniowych.
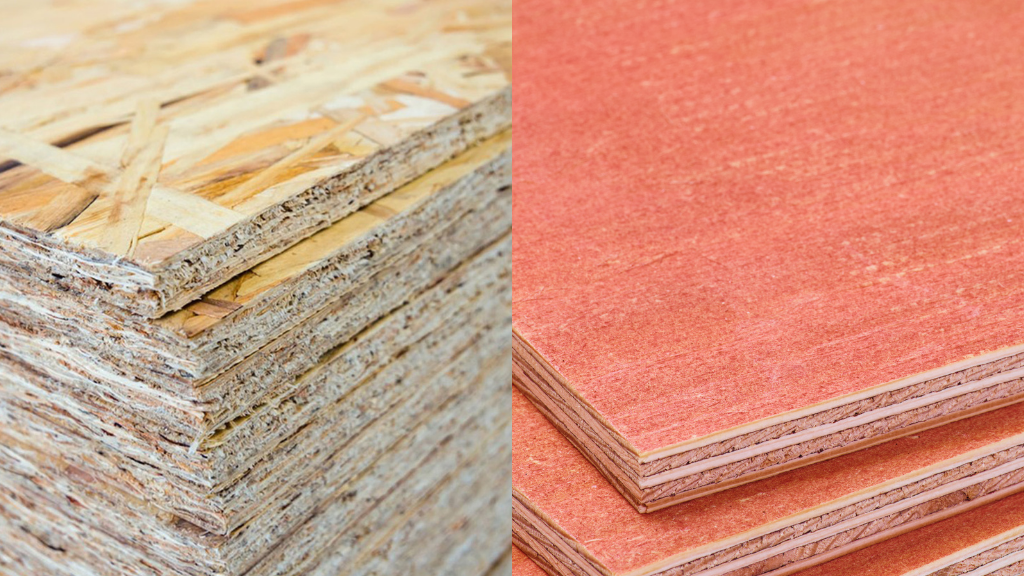
Porównanie OSB3 vs sklejka – kluczowe parametry w prefabrykacji
Dla szybkiego porównania cech zestawiliśmy najważniejsze parametry płyty OSB3 i sklejki w formie tabelarycznej. Warto pamiętać, że właściwości sklejki mogą się różnić w zależności od rodzaju (gatunek drewna, rodzaj kleju, klasa sklejki), a właściwości OSB – w zależności od producenta i grubości. Niemniej tabela obrazuje ogólne tendencje:
Cecha | Płyta OSB3 | Sklejka |
Struktura i wytrzymałość | Trójwarstwowa struktura z orientowanymi wiórami; sztywna, wytrzymała wzdłuż głównej osi (kierunkowa). | Wielowarstwowa konstrukcja z fornirów o krzyżowym układzie; bardzo wysoka wytrzymałość wzdłuż i w poprzek (bardziej jednolita). |
Nośność i odporność na ścinanie | Wysoka nośność przy zginaniu wzdłuż; dobra odporność na ścinanie, choć nieco niższa przy obciążeniach dynamicznych. | Bardzo wysoka wytrzymałość na zginanie, rozciąganie, ściskanie i ścinanie w płaszczyźnie; lepiej znosi obciążenia udarowe (dynamiczne). |
Precyzja obróbki CNC | Dobra obrabialność, lecz przy frezowaniu krawędzie mogą się strzępić; wióry mogą powodować postrzępione krawędzie przy cięciu. | Bardzo dobra – sklejka tnie się czysto, bez wyłamań (zwłaszcza gatunki o jednorodnej strukturze jak brzoza); stabilna wymiarowo przy skomplikowanej obróbce. |
Zachowanie na liniach Weinmann/Randek (automatyczna prefabrykacja) | Możliwa automatyczna obróbka i montaż (np. przy przykręcaniu/zbiciu do szkieletu), jednak OSB wymaga nieco większej ostrożności – np. precyzyjnego ustawienia osadzania zszywek/gwoździ, by uniknąć pęknięć krawędzi. | Świetnie sprawdza się na liniach zautomatyzowanych – płyta zachowuje stabilność, mniej narażona na wykruszanie krawędzi przy wbijaniu elementów mocujących; większy margines tolerancji przy drobnych odchyłkach maszyn. Możliwość użycia łączników do mocowania płyty bliżej krawędzi (zarówno gwoździ jak i zszywek) |
Odporność na wilgoć (klasa użytkowania) | OSB3 jest przeznaczona do środowiska wilgotnego (klasa 2, użytkowanie w warunkach o podwyższonej wilgotności) – klej wodoodporny zapewnia odporność na czasowe zawilgocenie. Krawędzie OSB wymagają zabezpieczenia przed wodą (skłonność do pęcznienia). | Zależy od typu sklejki: dostępne są sklejki wodoodporne (np. klasy BFU 100, oznaczane potocznie jako WBP) o bardzo wysokiej odporności na długotrwałe zawilgocenie, lepszej niż OSB3. Natomiast sklejki suchotrwałe nadają się tylko do wnętrz. |
Cena (orientacyjnie, 18 mm) | Niższa – ok. 20–40 zł/m² (OSB 3 w standardowym formacie). | Wyższa – ok. 60–90 zł/m² (sklejka liściasta, np. brzozowa, 18 mm). |
Dostępność dużych formatów | Bardzo dobra – standardowo płyty 2500×1250 mm, dostępne też większe formaty (np. 2800×2070 mm, a u niektórych producentów nawet dłuższe). Ułatwia to zastosowanie w prefabrykacji dużych paneli ściennych/dachowych. | Ograniczona – typowe maksymalne formaty to 1250×2500 mm (sklejka brzozowa, liściasta) lub do 1500×3000 mm (sklejki iglaste lub specjalne). Większość sklejki ma mniejsze arkusze niż OSB, co może wymagać więcej łączeń. |
Trwałość biologiczna (odporność na grzyby, pleśń) | Surowa płyta OSB zawiera dużo ligniny i żywic, ale w długotrwałej wilgoci może rozwijać pleśń na powierzchni. Wymaga zabezpieczeń, jeśli ma być eksponowana na czynniki zewnętrzne. | Sklejka wodoodporna ma wysoką odporność na biodegradację – fenolowe kleje są odporne na grzyby, a liściaste drewno (np. brzoza) jest stosunkowo trwałe. Niemniej każda sklejka wymaga impregnacji/ochrony w środowisku zewnętrznym. |
Wygląd i estetyka | Surowy, techniczny wygląd (wióry widoczne na powierzchni). OSB nie jest zwykle używana w miejscach ekspozycyjnych bez przykrycia, choć bywa stosowana dekoracyjnie we wnętrzach industrialnych. W OSB/3 oraz OSB/4 często dodatek emulsji parafinowej utrudnia malowanie powierzchni. | Naturalny wygląd drewna – usłojenie fornirów na powierzchni czyni sklejkę materiałem estetycznym i łatwym do malowania. Dostępne różne klasy jakości powierzchni (od konstrukcyjnej po meblową). Sklejka często wybierana do projektów, gdzie powierzchnia ma być widoczna i atrakcyjna. |
Zastosowanie jako płyta konstrukcyjna | Bardzo powszechne – OSB3 to standard w poszyciach ścian, podłóg i dachów domów szkieletowych, budynkach modułowych itp. Wybór OSB jest często podyktowany ekonomią – spełnia normy wytrzymałości przy niższym koszcie. | Uniwersalne, ale droższe – sklejka konstrukcyjna (np. sklejka szalunkowa, sklejka stolarska) również stosowana jest w ścianach, stropach, dachach, ale ze względu na wyższą cenę częściej używana jest tam, gdzie wymagana jest ponadstandardowa trwałość lub estetyka (projekty premium, obiekty wystawowe, elementy eksponowane). Nieco inaczej jest np. w USA gdzie jest dużo bardziej powszechnie stosowana niż np. w Polsce. |
Zalecane minimalne odległości łącznika od krawędzi zależą od kilku warunków: kierunku ułożenia włókien, obciążenia lub nie krawędzi, czy otwory były wcześniej nawiercone, średnicy łącznika i gęstości drewna. | Zalecana min. odl. 10 d | Zalecana min. odl. 5d |
Odporność na wyrywanie mocowań (siła trzymania gwoździ/wkrętów) | Nieco niższa – wiórowa struktura OSB może ulegać lokalnym wykruszeniom przy krawędzi pod wpływem dużych sił, zwłaszcza jeśli łącznik jest zbyt blisko brzegu. Przy wkręcaniu trzeba uważać, by nie „przestrzelić” wkrętu zbyt głęboko. | Bardzo wysoka – sklejka dzięki skrzyżowanym warstwom forniru świetnie trzyma gwoździe i wkręty. Łączniki nawet przy stosunkowo niewielkiej odległości od krawędzi mają mocne osadzenie w warstwach drewna. Płyta rzadziej pęka czy rozwarstwia się przy wbijaniu/wykręcaniu. |
Zalecana gęstość mocowań (rozstaw łączników na krawędziach) | Standardowo ok. 150 mm (15 cm) odstępu między gwoździami/śrubami na podporach/krawędziach. Gęstsze mocowanie (np. co 10 cm) może osłabiać krawędź OSB – należy sprawdzać wymagania projektu. | 100–150 mm – sklejka konstrukcyjna umożliwia zagęszczenie mocowań nawet co 10 cm na krawędziach, gdy wymagają tego obliczenia (np. ściany usztywniające przy dużych obciążeniach wiatrem). Jej krawędzie lepiej znoszą gęste mocowanie bez uszkodzeń. |
Paroprzepuszczalność (μ) | Współczynnik μ ~ 200 (sucha płyta, może wzrosnąć nawet do 300 przy niektórych gęstościach). OSB ma wysoki opór dyfuzyjny, zbliżony do folii paroizolacyjnej – działa prawie jak bariera dla pary wodnej. W praktyce płyta OSB słabo przepuszcza parę, co trzeba uwzględnić w projektowaniu warstw przegrody. | Współczynnik μ ~ 80-90 dla dużej wilgotności powietrza i 200-220 dla małej wilgotności powietrza. Sklejka ma niższy opór dyfuzyjny – lepiej przepuszcza parę wodną niż OSB. Dzięki temu “oddycha” bardziej jak naturalne drewno. Umożliwia to odparowanie wilgoci z przegrody, o ile warstwy są dobrze zabezpieczone przed kondensacją. |
Ślad węglowy (produkcja 1 m³) | Około 552 kg CO₂e/m³ (energia i żywice użyte do produkcji OSB generują taką ilość ekwiwalentu CO₂). Drewno użyte w płycie jednocześnie magazynuje biogeniczny węgiel, co może częściowo kompensować emisje. | Około 538 kg CO₂e/m³ (produkcja sklejki liściastej). Płyta sklejona z fornirów ma zbliżony rząd emisji do OSB. Uwaga: Drewno w 1 m³ sklejki magazynuje ok. 650–700 kg CO₂, co potencjalnie czyni ją materiałem o ujemnym bilansie węglowym (więcej CO₂ z atmosfery zmagazynowane niż wyemitowane). Jednak standardowe analizy LCA zwykle podają wartości bez uwzględnienia magazynowania biogenicznego. |
Zawartość kleju i emisja formaldehydu (klasy emisji) | Spoiwia: zwykle żywice syntetyczne bez dodatku formaldehydu (np. PMDI – poliizocyjanian) w rdzeniu oraz fenolowe na powierzchni. Dzięki temu płyty OSB3 w większości spełniają surowe normy emisji. Klasa E1 (≤0,124 mg/m³ wg EN 717-1) to standard – rzeczywiste emisje są na ogół znacznie niższe. Wiele płyt OSB ma certyfikat E0/NAF (no added formaldehyde), co oznacza, że emitują formaldehyd tylko na poziomie naturalnego drewna. | Spoiwia: w sklejce zależą od rodzaju – sklejki konstrukcyjne i zewnętrzne zazwyczaj klejone są żywicą fenolowo-formaldehydową (PF) o bardzo niskiej emisji (klej ten po utwardzeniu jest trwały i „zamknięty” w strukturze). Sklejki do wnętrz często klejone są żywicą mocznikowo-formaldehydową (UF/MUPF) o nieco wyższej emisji, ale nadal mieszczącej się w klasie E1 (≤0,124 mg/m³). Dostępne są też sklejki o ultraniskiej emisji – np. Paged GreenPly z klejem na bazie naturalnych biopolimerów, spełniająca klasę E0 (emisja formaldehydu poniżej 0,05 mg/m³). Podczas wyboru sklejki warto zwrócić uwagę na certyfikat emisji – najlepsze wyroby osiągają poziom emisji jak drewno naturalne. |
Klasa reakcji na ogień (EN 13501-1) | Standardowa płyta OSB jest materiałem palnym (drewno + żywica); najczęściej klasyfikowana w klasie D (d2, s1 lub s2 – średnie parametry dymienia). Dostępne są jednak płyty OSB FR (ogniochronne, np. z dodatkiem soli boru), które uzyskują klasę B-s2,d0 – czyli bardzo ograniczone palenie, średnie zadymienie, brak płonących kropli. | Sklejka standardowa również jest palna (zwykle klasa D-s2,d0). Dzięki impregnacji ogniochronnej można uzyskać sklejkę trudnozapalną – np. sklejka Paged FR osiąga klasę B-s1,d0 (bardzo ograniczone palenie, niska emisja dymu, brak płonących drobin). Osiągnięcie najwyższych klas niepalności (A1/A2) jest niemożliwe dla wyrobów z drewna bez specjalnych okładzin, ale klasa B jest możliwa dla obu materiałów tylko z specjalnymi okładzinami. |
Surowiec i ekologia | Produkowana głównie z drewna iglastego (tanie, szybko rosnące gatunki – sosna, świerk, topola) z tartacznych odpadów lub plantacji. Wykorzystanie drobnych wiórów pozwala zagospodarować surowiec niskiej jakości. Płyty OSB są uważane za materiał dość ekologiczny – składają się ~90% z drewna, reszta to kleje i wosk. Odpady OSB można poddać recyclingowi lub wykorzystać energetycznie. | Produkowana z pełnego drewna w postaci forniru – wymaga surowca wyższej jakości (duże prostoliniowe kłody). Sklejka liściasta (np. brzozowa) często pochodzi z kontrolowanych upraw leśnych. Podobnie jak OSB, sklejka jest w dużej mierze naturalna (ok. 90–95% drewna, reszta klej). Wersje z klejem bio są w pełni biodegradowalne. Oba materiały mogą posiadać certyfikat FSC/PEFC potwierdzający zrównoważone pochodzenie drewna. |
Certyfikacje jakości | Płyty OSB renomowanych producentów mają certyfikaty zgodności z normą EN 300 (np. oznaczenie OSB3), krajowe aprobaty techniczne oraz często ISO 9001. Dostępność w handlu jest szeroka – to materiał standardowy. | Sklejki konstrukcyjne również posiadają oznaczenia norm (np. EN 636, EN 314 – dotyczące właściwości i jakości klejenia). Wybierając sklejkę do konstrukcji, warto sprawdzić klasę użyteczności – techniczną (np. EN 636-2 dla środowiska wilgotnego) oraz certyfikat CE na zastosowania konstrukcyjne. Markowe sklejki (jak Paged) posiadają też certyfikaty ISO oraz atesty higieniczne. |
Jak widać z tabeli, sklejka wypada lepiej pod względem większości parametrów technicznych (wytrzymałość, obróbka, odporność krawędzi, estetyka, paroprzepuszczalność, stabilność wilgotnościowa), podczas gdy płyta OSB góruje nad nią ceną i dostępnością (co często bywa decydujące przy budżetowych realizacjach). OSB sprawdzi się dobrze jako typowy materiał konstrukcyjny tam, gdzie priorytetem jest niski koszt i szybki montaż, natomiast sklejka znajdzie zastosowanie w projektach wymagających ponadprzeciętnej trwałości, precyzji i wysokiej jakości wykończenia (np. moduły prefabrykowane o podwyższonym standardzie, obiekty użyteczności publicznej, elementy wystawiennicze itp.). Poniżej omawiamy bardziej szczegółowo wybrane aspekty porównania, istotne dla prefabrykacji maszynowej oraz wykonawców konstrukcji drewnianych.
Wytrzymałość i parametry konstrukcyjne
Wytrzymałość mechaniczna sklejki jest znacząco większa, dzięki jej budowie. Wielowarstwowa sklejka zachowuje dużą sztywność i nośność we wszystkich kierunkach płyty – cechuje ją wysoka odporność na zginanie, rozciąganie, ściskanie oraz ścinanie w płaszczyźnie. W testach porównawczych sklejka uzyskuje lepsze wyniki niż OSB tej samej grubości. Jest też bardziej odporna na obciążenia dynamiczne – uderzenia, wibracje – co ma znaczenie np. przy elementach narażonych na uderzenia lub w konstrukcjach narażonych na ruch (np. podesty sceniczne, moduły przenośne).
Płyta OSB3 również jest materiałem nośnym, zaprojektowanym do przenoszenia znacznych obciążeń. Dzięki długim wiórom i mocnej żywicy, OSB osiąga wysoką wytrzymałość na zginanie wzdłuż dłuższej krawędzi (tam, gdzie wióry są ułożone równolegle). Jej moduł sprężystości i wytrzymałość na rozciąganie wzdłużne są nieco niższe niż sklejki, ale w praktyce nadal spełniają wymagania konstrukcyjne dla domów i stropów. OSB wykazuje natomiast nieco słabszą wytrzymałość poprzeczną (wzdłuż krótszego boku) – zwykle około połowy wartości wzdłużnej, podczas gdy sklejka ma wytrzymałość w obu kierunkach zbliżoną. Oznacza to, że przy projektowaniu z OSB trzeba zwrócić uwagę na kierunek ułożenia płyty (dłuższy wymiar płyty OSB układać wzdłuż przęseł, prostopadle do podpór), podczas gdy sklejka jest bardziej uniwersalna pod tym względem.
W kontekście prefabrykacji budowlanej (np. produkcja paneli ściennych w fabryce) obie płyty spełniają normy nośności, jednak sklejka może oferować dodatkowy margines bezpieczeństwa w krytycznych miejscach. Przykładowo, sklejka konstrukcyjna brzozowa o grubości 12 mm może wykazywać nośność zbliżoną lub wyższą od OSB3 o grubości 15 mm czy 18 mm – co pozwala czasem zredukować grubość poszycia bez utraty wytrzymałości, kosztem wyższej ceny. W praktyce jednak OSB3 gr. 12mm i 22mm stały się standardem w ścianach i stropach prefabrykowanych, gdyż oferują wystarczającą wytrzymałość przy akceptowalnych kosztach.
Odporność na ścinanie (istotna np. dla tarcz usztywniających ścian) jest wysoka wytrzymałość u sklejki. W testach na ścianach usztywnionych poszyciem, sklejka osiąga wyższe parametry niż OSB, zwłaszcza po cyklach obciążeń powtarzalnych (sklejka lepiej zachowuje sztywność przy wielokrotnym obciążaniu).
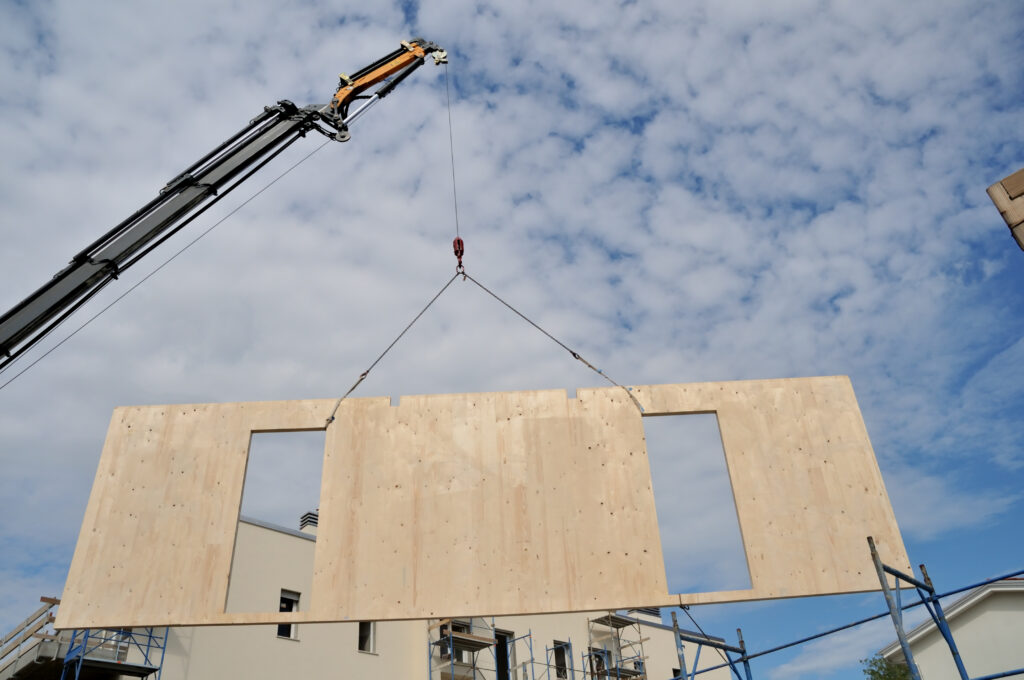
Obróbka maszynowa i precyzja (CNC)
Obróbka CNC i praca na zautomatyzowanych liniach montażowych to obszar, w którym jakość materiału ma duże znaczenie. Sklejka uchodzi za materiał bardziej przyjazny w obróbce – przy cięciu piłą lub frezowaniu CNC daje czystą krawędź, nie strzępi się nadmiernie (zwłaszcza sklejka z fornirów liściastych o gęstej strukturze). Można w niej precyzyjnie wycinać otwory, wpusty, otwory pod gniazda instalacyjne itp., zachowując dokładność wymiarów. Przy wierceniu i frezowaniu sklejka nie wykazuje tendencji do wyłamywania dużych odprysków. To czyni ją idealną do elementów prefabrykowanych wymagających dużej dokładności – np. paneli ścian z otworami okiennymi wycinanymi numerycznie.
Płyta OSB również może być obrabiana maszynowo, ale wymaga nieco więcej uwagi. Ze względu na wiórową strukturę, krawędzie po cięciu mogą być lekko postrzępione – czasem wymaga to dodatkowego szlifowania lub wykończenia krawędzi, jeśli będą widoczne. Przy wierceniu i frezowaniu CNC drobne kawałki wiórów mogą się wyrywać z krawędzi, co skutkuje mniej gładkim obrysem. W wielu zastosowaniach konstrukcyjnych (gdzie krawędź i tak będzie schowana) nie ma to znaczenia, ale np. przy prefabrykacji elementów modułowych wyposażonych w gniazda/otwory może to wymagać poprawek. Zaletą OSB jest natomiast brak wewnętrznych pustek czy sęków – obróbka jest przewidywalna, narzędzia tnące zużywają się podobnie jak przy sklejce.
Na liniach automatycznych do prefabrykacji obie płyty są szeroko stosowane. Maszyny te potrafią automatycznie przycinać panele, wiercić otwory oraz zszywać/gwoździować płyty do szkieletu. Z perspektywy maszyn:
- OSB jest bardziej jednorodna pod względem twardości, więc np. pistolety do gwoździ ustawione na stałą siłę wbijania zwykle działają powtarzalnie. Trzeba jednak uważać na odległości od krawędzi – automaty muszą być dobrze skalibrowane, by gwoździe lub zszywki nie trafiały zbyt blisko brzegu (ryzyko rozwarstwienia OSB).
- Sklejka ma warstwy o zmiennych kierunkach włókien, co czasem minimalnie wpływa na opór przy wbijaniu gwoździa. Jednak dzięki większej tolerancji materiałowej sklejka wybacza drobne błędy – nawet jeśli łącznik trafi blisko krawędzi, jest mniejsze ryzyko uszkodzenia. Automatyczne podajniki i piły radzą sobie ze sklejką bez problemu; ewentualne różnice w gęstości drewna między warstwami nie wpływają znacząco na proces.
Podsumowując: W produkcji maszynowej obie płyty są porównywalne, jednak sklejka zapewnia większy komfort i estetykę obróbki. Fabryki prefabrykatów często decydują się na OSB ze względu na koszt, ale tam gdzie priorytetem jest precyzja i brak poprawek, wybierają sklejkę. Przykładowo, w elementach, które pozostaną widoczne lub pół-odsłonięte (np. sufity modułowe, ściany wewnętrzne w systemach modułowych), sklejka da lepszy efekt wizualny i dokładność wykonania.
Odporność na wilgoć i warunki środowiskowe
Drewno i materiały drewnopochodne są wrażliwe na wilgoć – dlatego ważne jest, jak OSB i sklejka zachowują się przy zawilgoceniu oraz zmianach wilgotności otoczenia.
OSB3 jest klasyfikowana jako płyta do zastosowań w warunkach wilgotnych – oznacza to, że użyte kleje są wodoodporne (np. żywice poliuretanowe MDI i fenolowe), a sama płyta nie rozwarstwi się przy okresowym zawilgoceniu. Jednak OSB wciąż chłonie wodę przez niezabezpieczone krawędzie – przy bezpośrednim kontakcie z wodą (deszcz na budowie, wysoka wilgotność) pęcznieje, szczególnie na grubość. Typowa OSB3 może spęcznieć nawet o kilkanaście procent po 24h w wodzie (np. 15% wzrostu grubości). Po wyschnięciu większość tej deformacji nie ustępuje Dlatego w konstrukcjach szkieletowych zaleca się, by płyty OSB były zabezpieczone przed długotrwałym zamoknięciem (np. poprzez impregnację krawędzi i szybkie zamknięcie stanu surowego budynku).
Sklejka występuje w wersjach do użytkowania w warunkach suchotrwałych, podwyższonej wilgotności i wodoodpornych. Sklejka wodoodporna (klejona żywicą fenolową, spełniającą 3 klasę jakości sklejenia EN 314-2) potrafi wytrzymać nawet długotrwałe zanurzenie w wodzie bez rozwarstwienia – stąd stosuje się ją np. na poszycia łodzi, szalunki betonowe czy elewacje. Oczywiście drewno w niej zawarte nadal pęcznieje, ale istotne jest, że klej się nie rozpuszcza. Sklejka suchotrwała (na kleju mocznikowym) nie powinna być wystawiana na działanie wody – w warunkach prefabrykacji budynków używa się jej tylko wewnątrz suchych pomieszczeń. W kontekście OSB3 vs sklejka należy więc porównywać sklejkę wodoodporną z OSB3: tutaj sklejka zwykle wypada lepiej – dobre gatunkowo sklejki (zwłaszcza liściaste) mają wyższą odporność na długotrwałą wilgoć, mniejszy przyrost grubości i po które wchłonie wodę szybciej, bo ma wyższą porowatość.
W prefabrykacji elementów budowlanych istotne jest, że podczas montażu na placu budowy poszycia mogą zamoknąć (deszcz). Sklejka daje tu pewną rezerwę bezpieczeństwa – nawet jeśli powierzchniowo złapie wilgoć, nie osłabi to tak szybko połączeń i nie doprowadzi do trwałej deformacji. OSB3 również wytrzyma typową ekspozycję na deszcz (zgodnie z normą powinna przetrwać cykliczne nawilżanie), ale wymaga sprawniejszego osuszenia i ochrony przed ponawiającym się zawilgoceniem.
Odporność biologiczna: Wilgoć wiąże się też z ryzykiem rozwoju grzybów. Surowa płyta OSB zawiera resztki kory i drobne porowate przestrzenie, gdzie przy długotrwałym zawilgoceniu może pojawić się pleśń. Sklejka liściasta jest pod tym względem bardziej odporna – brzoza czy liściaste forniry mają naturalne właściwości antyseptyczne nieco lepsze niż wióry sosnowe, a do tego fenolowe spoiwo w sklejce zewnętrznej utrudnia rozwój grzybni. Ogólnie jednak żaden z tych materiałów nie jest odporny na warunki stałego zawilgocenia – wymagają obróbki chemicznej (impregnat) lub konstrukcyjnej (sucha obudowa) by służyć długo w trudnych warunkach.
Paroprzepuszczalność i „oddychanie” przegrody
Paroprzepuszczalność materiału określa współczynnik oporu dyfuzyjnego μ. Im wyższy μ, tym materiał bardziej hamuje przenikanie pary wodnej. W przypadku płyt drewnopochodnych μ zależy od gęstości i rodzaju spoiwa. Płyta OSB ma dość wysoki μ, podawany w szerokim zakresie ~100 do 300 (często przyjmuje się wartość ok. 200 jako reprezentatywną dla OSB/3). Oznacza to, że OSB jest średnio około 200 razy mniej przepuszczalna dla pary niż warstwa powietrza o tej samej grubości – innymi słowy stanowi barierę dla wilgoci unoszącej się w powietrzu. Dla porównania, folia paroizolacyjna PE ma μ > 100000, a więc OSB nie jest całkowitą paroizolacją, lecz jednak znacznie ogranicza dyfuzję. W ścianie szkieletowej poszytej od wewnątrz OSB może dojść do kondensacji, jeśli para wodna nie ma gdzie ujść – dlatego zaleca się stosować płyty OSB po wewnętrznej stronie przegrody (jako element hamujący ucieczkę pary do izolacji). Zewnętrzną stronę ściany lepiej wykończyć materiałem bardziej przepuszczalnym (np. płytą porowatą, membraną), by przegroda mogła wysychać na zewnątrz.
Sklejka ma niższy opór dyfuzyjny – jej μ jest zbliżony do litego drewna i wynosi zazwyczaj 50–70 dla sklejki suchej, a może wzrosnąć do ok. 100–150 gdy jest mocno zagęszczona lub wilgotna. To wciąż więcej niż np. wełna mineralna (μ ~1), ale znacznie mniej niż OSB. Oznacza to, że sklejka w przegrodzie pozwala na dyfuzję pary w pewnym stopniu. Mówi się, że ściana ze sklejką „oddycha” bardziej niż z OSB. W praktyce sklejka może być stosowana zarówno po wewnętrznej, jak i zewnętrznej stronie izolacji w szkielecie, o ile warstwy zostały poprawnie zwymiarowane pod względem fizyki budowli. Jeżeli zależy nam na wyższej paroprzepuszczalności ścian (np. w domach energooszczędnych bez foliowej paroizolacji, tzw. „open membrane” system), sklejka będzie lepszym wyborem na poszycie niż OSB. Trzeba jednak pamiętać o zabezpieczeniu sklejki przed bezpośrednią wilgocią zewnętrzną (np. wiatroizolacją), gdyż przepuszczając parę, jednocześnie chłonie wodę szybciej niż OSB.
Wnioski praktyczne: Płyty OSB/3 działają jak półparoizolacja, więc najlepiej umieszczać je od strony ciepłej (wewnętrznej) przegrody, co zapobiega napływowi wilgoci w izolację. Sklejka może pełnić rolę poszycia od strony zewnętrznej ściany, pozwalając konstrukcji wydzielać parę na zewnątrz – np. w domach szkieletowych z „oddychającymi” ścianami. Niemniej, nawet przy sklejce, warto stosować kontrolę pary (np. folie o zmiennym oporze) jeśli pomieszczenia generują dużo wilgoci. Sumarycznie, pod kątem prefabrykacji budynków: wybór OSB czy sklejki wpływa na strategię izolacji przeciwwilgociowej – OSB narzuca bardziej tradycyjne rozwiązanie (paroizolacja i wiatroizolacja), sklejka daje możliwość bardziej „diffusion open” podejścia, ale sama nie zastępuje membran całkowicie.
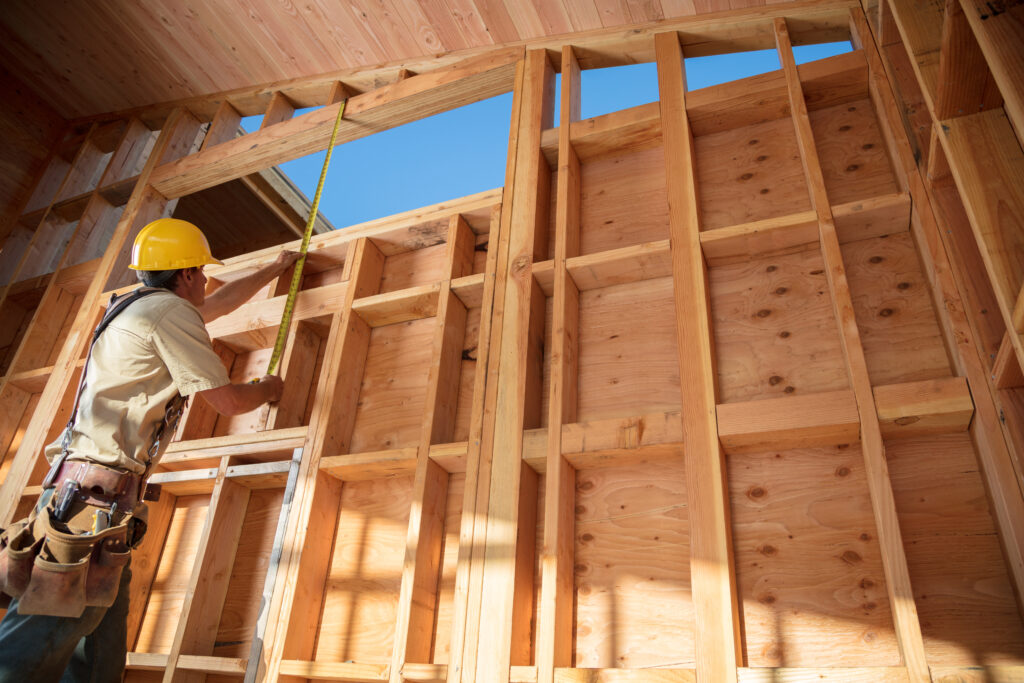
Emisja formaldehydu i klasy higieniczności
Zdrowie i ekologia materiałów budowlanych są dziś równie ważne jak ich właściwości techniczne. Zarówno sklejka, jak i OSB, produkowane są z dodatkiem klejów syntetycznych, co rodzi pytania o emisję formaldehydu (gaz będący składnikiem niektórych żywic, uznawany za szkodliwy w dużych stężeniach). W Unii Europejskiej obowiązują surowe normy ograniczające emisje z płyt drewnopochodnych – klasa E1 (zgodnie z EN 717-1) wymaga, by produkt uwalniał ≤ 0,124 mg formaldehydu na każdy m³ powietrza. Zarówno sklejka, jak i OSB renomowanych marek spełniają tę normę, a często mają emisje parokrotnie niższe.
Płyty OSB – ciekawostką jest, że większość OSB produkowana w Europie jest klejona bez użycia formaldehydu. Stosuje się żywice poliuretanowe (pMDI) i wosk, ewentualnie fenolowo-formaldehydowe warstwy zewnętrzne, które jednak emitują znikome ilości gazu (fenolowe kleje „wiążą” formaldehyd chemicznie). W efekcie wiele płyt OSB może pochwalić się statusem NAF (No Added Formaldehyde) albo bardzo niskimi wynikami – np. EGGER OSB oznaczane są jako E0 (emisja na poziomie naturalnego drewna). To sprawia, że OSB nadaje się do pomieszczeń mieszkalnych i jest zwolniona z niektórych regulacji dotyczących formaldehydu w wyrobach budowlanych. Oczywiście zawsze pozostaje pewna emisja z samego drewna (drewno samo w sobie zawiera śladowe ilości formaldehydu), ale są to ilości pomijalne z punktu widzenia zdrowia.
Sklejka – tutaj sytuacja zależy od rodzaju użytego kleju:
- Sklejki konstrukcyjne zewnętrzne (wodoodporne) klejone są zwykle żywicą fenolowo-formaldehydową (PF). Ten klej po pełnym utwardzeniu ma bardzo niską emisję (większość wolnego formaldehydu zostaje związana w strukturze chemicznej). Dlatego dobre sklejki wodoodporne również bez problemu mieszczą się w klasie E1, a często osiągają połowę dopuszczalnego poziomu lub mniej.
- Sklejki wewnętrzne (suchotrwałe) są często klejone żywicą mocznikowo-formaldehydową (UF), która niestety jest bardziej emisjogenna. Jednak technologia produkcji poszła do przodu – obecnie nawet na klejach UF sklejki mogą spełniać wymagania E1. Istnieją też odmiany sklejki klasy E0 – np. produkty oznaczone jako Ultra-Low Emission – gdzie stosuje się modyfikowane żywice o obniżonej zawartości formaldehydu.
- Na rynku pojawiają się sklejki bezformaldehydowe, klejone np. żywicami poliuretanowymi lub innymi bio-spoiwami. Przykładem jest wspomniana Paged GreenPly, w której wykorzystano naturalny klej na bazie bio-surowców (wolny od formaldehydu). Tego typu sklejka ma zerową emisję dodanego formaldehydu – emituje jedynie to, co samo drewno (czyli poziom czystego drewna).
W praktyce, jeśli nasz projekt prefabrykowany ma wysokie wymagania ekologiczne lub jest przeznaczony do wnętrz (np. moduły mieszkalne, meble), warto wybrać płyty o potwierdzonej niskiej emisji. Zarówno OSB, jak i sklejkę, możemy dostać z certyfikatem CARB Phase 2 / EPA (amerykańskie normy ultra niskiej emisji) lub europejskim E1/E0. W Polsce większość sklejki i OSB jest klasy E1, więc bezpieczna w użytkowaniu. Dla porównania – w latach 80-90 popularne płyty wiórowe miały dużo wyższe emisje (klasa E2), co obecnie jest wyeliminowane w materiałach konstrukcyjnych.
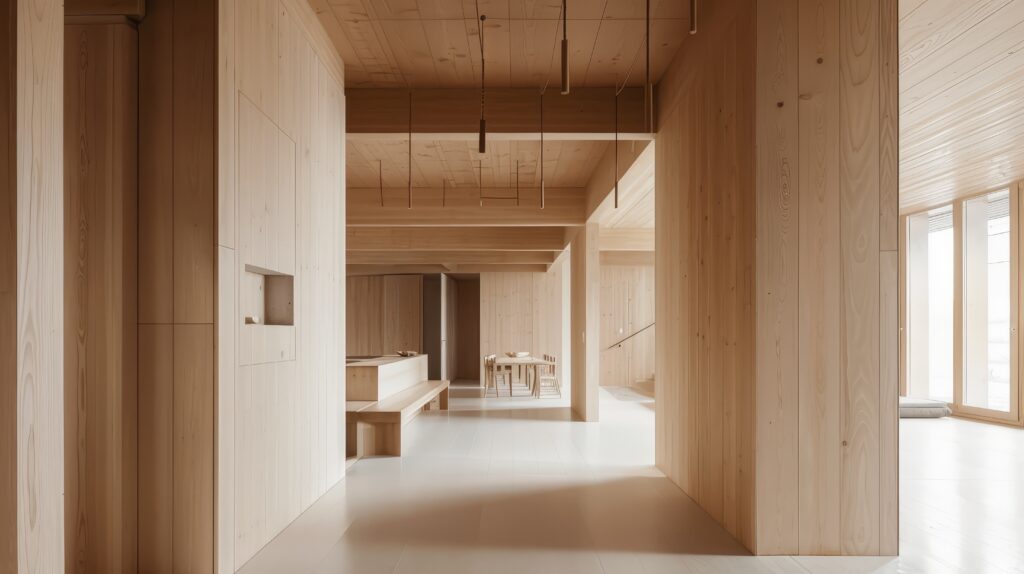
Klasy reakcji na ogień i bezpieczeństwo pożarowe
Pod względem ogniowym zarówno sklejka, jak i OSB są materiałami palnymi (to w 90% drewno). Surowe, nieimpregnowane płyty drewnopochodne zazwyczaj uzyskują klasę reakcji na ogień D (łatwo zapalne), czasem nawet E. Oznacza to, że przy pożarze materiał się pali, przyczyniając się do rozwoju ognia, i wydziela dym (s2 lub s3 – umiarkowane/duże zadymienie). Dla zastosowań konstrukcyjnych we wnętrzach (np. poszycia ścian w budynkach użyteczności publicznej) taka klasa bywa niewystarczająca, stąd rozwój płyt ognioodpornych.
Płyta OSB FR – niektórzy producenci oferują OSB z dodatkami przeciwogniowymi (np. impregnat w masie płyty). Taka płyta może osiągnąć klasę B-s1, d0 tak jak sklejka FR, czyli jest trudnozapalna – nie podtrzymuje ognia po odjęciu płomienia, dymienie na poziomie s2 (średnie), nie kapią płonące krople (d0). To porównywalna klasa do np. trudnozapalnych sklejonych paneli meblowych czy niektórych płyt gipsowych. OSB FR nadal jest materiałem drewnianym, więc w wysokich temperaturach ulega zwęgleniu, ale wolniej inicjuje pożar.
Sklejka ogniochronna (FR) – analogicznie, sklejkę można zaimpregnować środkami ogniochronnymi (ciśnieniowo lub powierzchniowo) albo wyprodukować z dodatkiem soli reagujących w ogniu. Sklejka Paged FR uzyskuje klasę B-s1,d0 (czyli niezapalna, z bardzo małą ilością dymu i bez płonących kropli). Sklejka może zatem wydzielać mniej dymu podczas pożaru. Są też dostępne sklejki o klasie Bfl-s1 (dla podłóg). Co ważne, jeśli sklejka/OSB ma być wykorzystana jako okładzina ścian wewnętrznych w drogach ewakuacyjnych, często wymaga się właśnie klasy minimum B-s1,d0 zgodnie z przepisami – tu częściej stosuje się sklejkę FR, bo łatwiej osiągnąć s1.
Zwykłe zastosowania: W domach jednorodzinnych i większości hal przemysłowych użycie surowej sklejki czy OSB jest dopuszczalne (klasa D). Drewno w konstrukcjach reaguje na ogień przewidywalnie – zwęgla się tworząc warstwę izolacyjną. W projektowaniu bierze się pod uwagę tempo zwęglania elementów drewnianych, by zapewnić odpowiednią odporność ogniową. Same płyty nie są traktowane jako elementy ogniochronne, a wręcz wymagają zabezpieczenia (np. gładź gipsowa, płyta GKF) jeśli potrzebna jest wysoka odporność ogniowa przegrody. Przy wyborze między OSB a sklejką standardową nie ma dużej różnicy – obie zachowują się podobnie w pożarze. Jeśli jednak zależy nam na wyższej klasie niepalności, oferta sklejki FR bywa szersza (różne grubości z certyfikatami B-s1,d0).
Podsumowując, w kontekście prefabrykacji: dla modułów i elementów budynków o zaostrzonych wymaganiach ppoż. (np. hotele, szkoły) lepiej postawić na sklejkę trudnozapalną, aby spełnić normy. W zwykłych domach i obiektach OSB/3 spełni swoją rolę, pamiętając że musi być zastosowana zgodnie z zasadami ochrony przeciwpożarowej (np. osłonięta od wewnątrz płytą g-k lub innym materiałem niepalnym, jeśli wymagane).
Wpływ na środowisko – ślad węglowy i zrównoważony rozwój
Oba materiały są uznawane za stosunkowo ekologiczne w kontekście budownictwa, głównie dlatego, że bazują na drewnie – surowcu odnawialnym, który w trakcie wzrostu wiąże dwutlenek węgla z atmosfery. Jednak produkcja przemysłowa pociąga za sobą emisje.
Ślad węglowy liczony jako emisja gazów cieplarnianych przy produkcji 1 m³:
- Dla OSB/3 szacuje się go (w zależności od źródła) na około 500–600 kg CO₂e/m³. Nasze dane (552 kg CO₂e/m³) mieszczą się w tym zakresie – dotyczą prawdopodobnie europejskiej produkcji z uwzględnieniem pozyskania drewna i energii w fabryce.
- Dla sklejki dostępne analizy wskazują wartości rzędu 500–550 kg CO₂e/m³ dla sklejki brzozowej niepowlekanej. Podana wartość ~538 kg CO₂e/m³ jest więc typowa. Warto zauważyć, że sklejka liściasta wymaga więcej energii na skrawanie fornirów i suszenie, ale z drugiej strony OSB zawiera nieco więcej kleju syntetycznego – te efekty się równoważą.
W powyższych liczbach nie uwzględniono jednak istotnego faktu: biogenicznego węgla w drewnie. 1 m³ drewna to około 250–300 kg pierwiastka węgla, co odpowiada 900–1100 kg CO₂ zmagazynowanego z atmosfery. Jeśli płyta będzie długo użytkowana, ten węgiel jest wyłączony z obiegu – w pewnym sensie budując z drewna, magazynujemy CO₂ w budynkach. Niektórzy producenci sklejki podają, że ich płyty magazynują ok. 650–700 kg CO₂/m³, co czyni je materiałem o potencjalnie ujemnym bilansie węglowym. Oczywiście to podejście zależy od założeń (standardowe LCA zwykle podają bilans dodatni, bo liczą tylko emisje z produkcji). Niemniej, faktem jest, że wybór drewna zamiast materiałów mineralnych czy metalowych znacznie obniża ślad węglowy budynku.
Z punktu widzenia prefabrykacji: firmy stawiające na zrównoważony rozwój często promują użycie sklejki lub OSB z certyfikatem FSC/PEFC, co gwarantuje, że drewno pochodzi z legalnych, odnawialnych źródeł. Ilość odpadów przy produkcji prefabrykatów z płyt jest minimalizowana (docinanie CNC pozwala optymalnie zużyć formatki). Często offcuty OSB/sklejki są wykorzystywane np. jako opał do ogrzewania fabryki, więc nic się nie marnuje – to wpisuje się w ideę gospodarki o obiegu zamkniętym.
Warto wspomnieć, że sklejka wymaga drewna wyższej jakości (grubsze kłody) niż OSB, które może powstawać z cieńszych drzew. Z jednej strony OSB efektywniej wykorzystuje surowiec (np. topolowe plantacje), z drugiej strony uprawy brzozy czy sosny na sklejkę też są odnawialne. W bilansie ekologicznym żaden z materiałów nie odstaje negatywnie – oba są lepsze niż np. beton pod względem emisji. Decydując OSB vs sklejka, można więc kierować się bardziej właściwościami technicznymi i kosztami, mając pewność, że budownictwo drewniane jest przyjazne klimatycznie.
Montaż i zalecenia wykonawcze (łączniki, mocowanie)
Sposób montażu płyt na konstrukcji wpływa na trwałość i sztywność całego elementu. Tutaj ujawniają się pewne praktyczne różnice między OSB a sklejką, wynikające z ich struktury.
- Łączniki mechaniczne (gwoździe, wkręty, zszywki): Sklejka dzięki budowie warstwowej ma lepszą zdolność utrzymania łączników – stanowi większy opór przy osiowym wyciąganiu wkrętów niż OSB o porównywalnej gęstości. W OSB wkręt trzyma głównie przez tarcie w sprasowanych wiórach; jeżeli siła wyrwania jest duża, może wyrwać fragmenty wiórów. W testach wychodzi, że sklejka ma wyższą wytrzymałość na wyrywanie wkrętów z krawędzi i powierzchni niż OSB (coś, co potwierdzają wykonawcy praktycy). Dlatego tam, gdzie spodziewane są duże obciążenia punktowe na łącznikach (np. mocowanie ciężkich zawieszeń do poszycia), sklejka daje większą pewność.
- Minimalna odległość od krawędzi: Jak wspomniano w tabeli, dla OSB zaleca się min. 8–10 mm od krawędzi płyty, żeby przy wbijaniu nie zrobić wyszczerbienia. Dla sklejki często wystarcza 6 mm. Przy automatycznym gwoździowaniu (np. taśmy gwoździ do pistoletu) warto zaprogramować linię tak, by gwoździe strzelać nie bliżej niż np. 15 mm od brzegu OSB i 10 mm od brzegu sklejki – to zapewni margines bezpieczeństwa. Sklejka w warsztacie stolarskim bywa nawet zszywana 5 mm od krawędzi bez problemu, ale to przy założeniu, że krawędź jest idealnie prostopadła i zszywka o odpowiedniej długości.
- Rozstaw mocowań (gęstość): Dla typowego poszycia konstrukcyjnego (np. ściany usztywniającej) przepisy wymagają gwoździ co ok. 15 cm na krawędziach i 30 cm w polu – i to dotyczy zarówno OSB, jak i sklejki. Jeśli jednak projekt zakłada bardzo duże obciążenia (strefy huraganowe, ściany budynków wielokondygnacyjnych), czasem stosuje się zagęszczenie gwoździ nawet co 10 cm na krawędziach. Sklejka lepiej to znosi – można nabić gęściej bez pękania krawędzi. OSB przy takim zagęszczeniu może miejscami się rozwarstwiać (wióry między bliskimi zszywkami mogą się rozchodzić). Dlatego w konstrukcjach najwyższej klasy, np. modułach, które muszą wytrzymać transport i montaż (wibracje, podnoszenie), wykonawcy nieraz decydują się na sklejkę i gęstsze przybicie, by mieć pewność sztywności połączeń.
- Gwoździe vs wkręty: OSB jest na tyle gładka i twarda, że gwoździe zwykłe trzymają się dobrze (zwłaszcza pierścieniowe). W sklejce gwoździe również trzymają świetnie; dodatkowo sklejka lepiej współpracuje z wkrętami samonawiercającymi – wkręt rozgina warstwy, które „zaciskają się” na gwincie. W OSB wkręt może czasem przestrzelić za głęboko (zwłaszcza używając wkrętarek pneumatycznych – OSB ma mniejszy opór początkowy, więc łatwo przesadzić). Dlatego zaleca się ustawienie ogranicznika głębokości lub stosowanie gwoździarki dla OSB, aby wszystkie łączniki miały jednakową głębokość i nie osłabiły struktury.
- Klejenie i uszczelnianie: Jeśli elementy prefabrykowane wymagają uszczelnienia połączeń (np. taśmy, kleje konstrukcyjne na stykach płyt), to zarówno OSB, jak i sklejka, mają dość podobną kompatybilność. Kleje poliuretanowe i akrylowe dobrze przylegają do obu powierzchni, choć OSB jest bardziej chłonna na krawędziach – warto zagruntować lub nałożyć więcej kleju, by dobrze wypełnić nierówności wiórów. Sklejka ma krawędź gładszą, łatwiej równomiernie pokryć klejem. W prefabrykacji często stosuje się frezowane krawędzie (pióro-wpust) – tu OSB ma przewagę, bo producenci oferują OSB/3 z pióro-wpustem, co ułatwia łączenie na budowie. Sklejka rzadziej ma takie wykończenie krawędzi fabrycznie i jeśli jest potrzebne, trzeba je frezować samodzielnie w zakładzie.
Dostępność wymiarów, logistyka i różnice cenowe
Jak już wspomniano, OSB jest dostępna w większych formatach i praktycznie w każdym składzie budowlanym. Standard to płyty 1250×2500 mm (lub 1245×2475 mm – zależnie od kraju), co odpowiada 3,125 m². Wielu producentów oferuje też dłuższe płyty – np. 2,8×2,07 m, a nawet szpachle OSB (ciągłe pasy) długości do 7–8 m na specjalne zamówienia. Dla fabryk domów prefabrykowanych duże formaty są plusem – pozwalają pokryć całą wysokość ściany jednym arkuszem, minimalizując łączenia i usztywniając konstrukcję na całej długości. OSB jest też tańsza – można kupować hurtowo duże ilości bez drastycznego obciążenia budżetu.
Sklejka w dużych formatach (np. 1500×3000 mm) jest trudniej dostępna i droższa jednostkowo. Najczęściej stosuje się klasyczny format 1250×2500 mm lub mniejsze (1220×2440 mm – typowy dla sklejki importowanej). W prefabrykacji oznacza to, że przy standardowej wysokości ściany ~2,7 m, jedna płyta 2500 mm nie wystarczy – trzeba robić poziomy styk lub zamawiać rzadkie formaty. Niektóre firmy radzą sobie, stosując sklejkę fornirowaną krzyżowo innego typu (np. płyty LVL lub MFP), ale to poza zakresem tego artykułu.
Cena pozostaje jednym z głównych czynników wyboru:
- OSB jest kilkukrotnie tańsza od sklejki liściastej. Różnica ~3x na m² (jak w tabeli: 30 zł vs 75 zł) powoduje, że przy dużych inwestycjach budżetowych OSB staje się naturalnym wyborem. Za cenę jednej sklejki 18 mm można kupić trzy OSB 18 mm – to przemawia do inwestorów przy budowie całych osiedli domów czy hal.
- Sklejka występuje w różnych gatunkach – tańsza sklejka iglasta (np. sosnowa) może kosztować mniej, często ok. 40–50 zł/m² przy grubości 18 mm. Jej właściwości techniczne są nieco słabsze niż w przypadku sklejek liściastych, ale nadal przewyższają parametry płyt OSB. Różnicę w cenie można dodatkowo zniwelować, wybierając cieńszą sklejkę – ponieważ płacimy za metr sześcienny materiału. Przykładowo: jeśli na podłogę stosujemy płytę OSB o grubości 22 mm, to w jej miejsce można użyć sklejki o grubości 18 mm. Mimo mniejszej grubości, sklejka wciąż zapewni odpowiednią wytrzymałość..
- Przy projektach premium cena schodzi na dalszy plan wobec wymagań jakościowych. Wtedy sklejka – mimo ceny – jest wybierana ze względu na swoje atuty. W przeliczeniu na cały budynek, koszt poszycia ze sklejki zamiast OSB podniesie koszt całości inwestycji jedynie o kilka procent, co czasem jest akceptowalne w zamian za np. lepszą trwałość czy wygląd.
Logistyka: Zarówno sklejka, jak i płyta OSB są łatwe w transporcie i składowaniu. OSB jest jednak mniej wrażliwa – nie zawiera fornirów, które mogłyby się rozwarstwić, i zazwyczaj pakowana jest w większe paczki, co ułatwia transport całych stosów wózkiem widłowym.
Oba materiały należy składować równo, na stabilnych podpórkach (np. paletach), ponieważ przy długim magazynowaniu mogą się odkształcać (wyginać).
W zakładach prefabrykacji, gdzie pracuje się z dużymi formatami, nie ma to jednak większego znaczenia – zarówno palety ze sklejką, jak i z OSB można przechowywać i podawać na linię produkcyjną w podobny sposób.
Wnioski – co wybrać do prefabrykacji i konstrukcji?
Wybór między sklejką a płytą OSB zależy od priorytetów projektu. Oba materiały mają ugruntowaną pozycję w budownictwie szkieletowym i prefabrykacji budowlanej, dlatego zamiast pytania „który jest ogólnie lepszy”, warto zapytać: który będzie lepszy dla mojego zastosowania?
Sklejka jest lepsza jakościowo – oferuje wyższą wytrzymałość (ok. 7–10% większą niż OSB), większą trwałość i odporność na uszkodzenia oraz estetykę, której OSB nie zapewnia. Jest idealna do projektów premium lub ekspozycyjnych: moduły mieszkalne o podwyższonym standardzie, wnętrza gdzie poszycie będzie widoczne (lub wykończone jedynie lakierem), konstrukcje wystawiennicze, meble wbudowane itp. W automatycznej obróbce CNC sklejka daje dokładność i powtarzalność, co przekłada się na mniejszy odpad i brak potrzeby poprawek. Dla wykonawców oznacza też łatwiejszy montaż (mniej pękających krawędzi, możliwość gęstszego gwoździowania). Wadą pozostaje cena – sklejka to materiał premium, więc używanie jej na masową skalę podnosi koszty produkcji.
OSB sprawdza się w budownictwie ekonomicznym – tam, gdzie liczy się niski koszt i szybka realizacja, a aspekt wizualny jest drugorzędny (bo np. poszycie i tak zostanie zakryte warstwami wykończeniowymi). W elementach nieeksponowanych, jak poszycia ścian od zewnątrz, poszycia dachowe pod papę, podłogi pod panele – OSB w zupełności spełnia swoją rolę. Przy dużej skali produkcji (np. fabryka domów modułowych budująca setki jednakowych segmentów) oszczędność na materiale może być na tyle znacząca, że uzasadnia wybór OSB i ewentualne dodatkowe zabiegi (np. szlifowanie krawędzi czy staranniejszy montaż). OSB ma też tę zaletę, że jest szeroko dostępna – w razie nagłej potrzeby łatwiej dokupić brakujące palety niemal w każdym składzie.
Prefabrykacja maszynowa: Na nowoczesnych liniach obróbki zautomatyzowanej obie płyty sprawują się dobrze i można założyć, że pod względem technologicznym są zamienne. Jeśli jednak fabryka celuje w najwyższą jakość produktu finalnego, może preferować sklejkę ze względu na margines tolerancji – np. jeśli robot minimalnie chybi z pozycją zszywki, sklejka to wybaczy, OSB może nadkruszyć krawędź. Sklejka daje też pewność co do parametrów każdej partii – renomowane sklejki mają mniejsze wahania gęstości, wilgotności i innych cech, podczas gdy OSB od różnych producentów potrafią się nieco różnić (np. jedne są bardziej miękkie, inne twardsze do wbijania gwoździ). Dlatego niektóre firmy prefabrykacyjne konsekwentnie używają sklejki mimo ceny, budując markę na jakości.
Zastosowania mieszane: W praktyce nic nie stoi na przeszkodzie, by w jednym obiekcie użyć obie płyty w komplementarny sposób. Np. w ścianach zewnętrznych dać sklejkę (dla lepszej paroprzepuszczalności i wytrzymałości na wiatry), a w wewnętrznych OSB (tańsza i działa jako paroizolacja). Albo użyć OSB do większości poszyć, a sklejki tylko tam, gdzie potrzebne są jej atuty (np. strefy przykręcania ciężkich elementów, okolice otworów okiennych dla lepszej odporności na rozrywanie, itp.). Takie podejście może zoptymalizować koszt vs korzyści.
Na koniec, z perspektywy klienta firm prefabrykacyjnych (dewelopera, inwestora):
- Jeśli budżet jest napięty – OSB/3 będzie rozsądnym wyborem: zapewni solidność konstrukcji przy niższej cenie. Trzeba tylko dopilnować, by wykonawca właściwie zabezpieczył i zamontował te płyty (szczeliny dylatacyjne, folie paro- i wiatroizolacyjne, itp.).
- Jeśli stawiasz na jakość i trwałość – warto rozważyć dopłatę do sklejki. Szczególnie w elementach, które mają służyć wiele lat w zmiennych warunkach (np. domek prefabrykowany przenoszony z miejsca na miejsce, kontenery mieszkalne, budynki wystawowe). Sklejka zapewni dłuższą żywotność bez degradacji parametrów oraz lepszy mikroklimat (mniej problemów z wilgocią).
- Przy konstrukcjach wymagających certyfikatów (np. ekologicznych, ogniowych) – częściej spełni je sklejka (dostępna w wariantach NAF, FR itp.). OSB również ma swoje „specjalne” odmiany, ale wybór jest mniejszy.
Podsumowując, sklejka vs OSB to trochę jak jakość vs ekonomia. Sklejka – materiał z „wyższej półki” – będzie najlepsza, gdy liczy się bezkompromisowa jakość, precyzja i trwałość. OSB/3 – „wołek roboczy” – wystarczy w większości standardowych zastosowań konstrukcyjnych, zwłaszcza tam, gdzie chodzi o szybciej, taniej, ale wciąż wystarczająco dobrze. Warto tę decyzję skonsultować z projektantem konstrukcji i wykonawcą prefabrykatu – oni uwzględnią specyfikę projektu, warunki użytkowania i wymagania normowe, pomagając dobrać idealny materiał dla Twojej inwestycji. Dzięki temu Twój budynek prefabrykowany będzie zarówno solidny, jak i opłacalny, niezależnie czy postawisz na sklejkę czy płytę OSB.